The top, or soundboard, is the most important contributor to the sound of the guitar. The critical factors seem to be that the top wood is stiff, yet light, and able to transmit sound without absorbing all of the sound energy. Traditionally, spruces are used due to their very high stiffness-to-weight ratios. And their ability to transmit sound quickly from end to end, their velocity.
Some woods soak up sound and produce a dull thud when stuck. This is damping, which has uses in lutherie, but not for top woods. Other woods are resonant, crisp, and ring with a “bell-like” tone. The longer the ring, the greater the sustain. Sustain is a good thing.
Since the 1960s, Western Red Cedar has been used for guitar tops — chiefly for nylon-string guitars — and has gotten very popular in the last ten years. It tends to have a darker sound than spruce, and it also tends to have a more complex tone, with more harmonic content, than the typically-used-by-factories Sitka Spruce. In the last five years or so, California Redwood has become known as a good alternative top wood, with the usual comment being that it has a tone between spruce and cedar. I’d like to get the brightness of spruce and the harmonic complexity of cedar out of this, so redwood it is.
The “buckskin” redwood top from Rick Micheletti was purchased circa 2009. The two bookmatched halves were glued together in 2011. It was sanded to a thickness pretty close to final, 0.118 inches, so it is ready to have the rosette installed. Here’s a photo of a few rosettes I’ve made that didn’t make it into finished guitars. I really like Brent McElroy’s rosettes and have basically copied his style. J. S. Bogdanovich also uses a similar treatment on his awesome nylon-string guitars. I’d suppose they have influenced a lot of builders in this area.

Maple rosettes in Western Red Cedar soundboards. The left and center rosettes are spalted maple, the right is a maple burl.
I don’t have any spalted maple that is as nice as the one on the left above. My choices for this are pretty limited. Here’s a shot of the rosette woods that I have ready to go at this point:
I didn’t love any of these. Not enough contrast with the top or just the wrong color. On this guitar we’ll go with some East Indian Rosewood, and trim it out with a couple bands of maple/bloodwood/maple purfling. Here’s the materials:
The rosewood is sanded down to about 1/10 inch on the drum sander in preparation for cutting. The rosewood donut is cut out with a Dremel tool attached to a couple of Stewart-McDonald appliances as shown below. The rosette channel is cut with the same tool. Theoretically, this becomes a very simple exercise because the bit used to cut the rosette is the same width as our maple/bloodwod/maple purfling. Measure twice and you’re done. Here’s an illustration of the procedure:
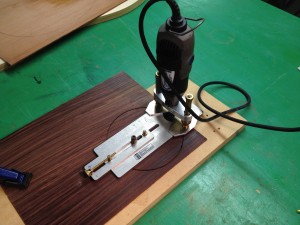
The lower board has a 3/16ths-inch pin sticking up and the rosewood has a hole in it that fits snugly around the pin. The Dremel rotates on the pin to cut the donut.

The soundboard has a coating of shellac to help prevent the dremel from tearing out the wood fibers. It has its own backing board with a 3/16ths center pin.

The Dremel is lifted from the rosewood board after routing the outer line of the donut and that same diameter setting is used to make the outside channel of the rosette.

The inside diameter of the rosewood cutout is then used to route the inside channel. Here’s the 1/16-inch router bit and the pin. Already cut are the inside and outside inlay channels. We’re switching over to a larger bit to dredge out the channel.
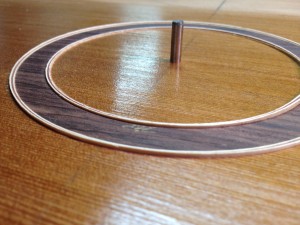
A tight fit is desired, but not so tight that glue-swollen wood will no longer fit into the channel. A real Goldilocks moment. So getting everything in before the glue starts to gel is always exciting.
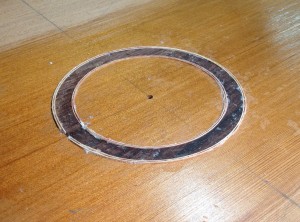
It seems like half an hour, but five minutes later all the parts are squeezed in and everything looks good.

Cover the rosette with something heavy until the glue dries. In this case, heavy is a piece of granite.
The main thing to be aware of if you use this rosette inlay method is that you need to be diligent in making sure that all of the rosette parts are well seated in the trough. If the fit is too tight, there will be sat least one piece that doesn’t go all the way in. This will not show up until you are sanding the top prior to finishing and you sand through part of the rosette and uncover an empty channel. So be careful and make sure none of the rosette parts are sticking up too much in any area. If you can make all of the rosette parts the same thickness, you’ll have a good way of knowing that everything is seated properly.
– – – – – – – – – – – –
There are a lot of methods people use to determine their idea of proper thickness for a guitar top. This is important because the top has to withstand years of constant pressure being applied by the strings — something close to 150 pounds of tension — yet it also needs to be light enough to be set into motion by a pluck of the strings. Getting this balance right is one of the critical things in being able to make consistently good guitars. Some people can flex a raw top and know from experience whether it is stiff enough to make a fine guitar and intuitively know how thick it should be for optimum sound. Others employ more scientific methods for repeatability. Some probably use voodoo. I use a couple of sticks and a five-pound weight to determine the top thickness. I’ve read that other people do similar things and this seems like an easy way to test stiffness. Gotta start somewhere. Let’s fire up the drum sander and thin this top until it deflects 1/4 inch under a five-pound weight. Like this:
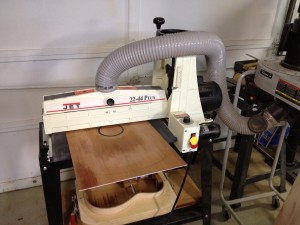
Sanding the front and back of the soundboard, taking off miniscule amounts to reach the target deflection point.
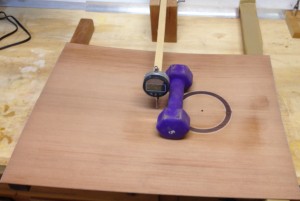
A five-pound weight is centered on the soundboard and the distance this causes the board to flex is recorded by the gauge.
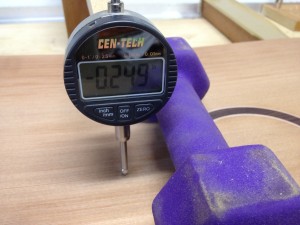
Sanding the top a tiny bit at a time getting to the target deflection point, which is 0.25 inch in this case. We’re there.
I read somewhere that precision is actually a measure how closely you can get the same result with a particular test run multiple times, i.e. repeatability. This is not a precise test. Also, I’ve noticed that the deflection changes if you turn the top over and measure from the back. I want to keep this simple, so let’s just say that all of the tests indicate that we are one thousandth of an inch from our target of .25 inches, just like in the photo.
One of the things I’m doing to understand/control my materials is measuring them. This piece of redwood is 17.25 inches wide and 22.06 inches long for an area of 380 square inches. The final thickness is 0.11 inches. This gives us a volume of 41.86 cubic inches. It weighs 303 grams or 10.69 ounces. So the weight number I use to compare this with other top woods is .255 ounces per cubic inch or 7.24 grams per cubic inch. This is pretty heavy compared to Wester Red Cedars that I have, but not far from my spruces. The best guitar I’ve built used cedar that weighed about 4 grams per cubic inch. My other cedar tops weigh about 25% more than that one. I’m recording the deflection numbers, but, since I don’t have a uniform width/length of the plate being measured, it’s not a good one-to-one comparison number. This piece seems very lively and has a glassy tap, so it should make a good guitar even if it’s almost twice as heavy as that one perfect piece of cedar that I used on the last OM.
There’s only two more things to do with this soundboard before letting it sit while we work on the sides: gluing a soundhole reinforcement patch to the inside and cutting the soundhole out. The soundhole reinforcement is a thin donut of spruce, or cedar or redwood, that is glued to the back of the top. The reinforcement patch is going on because this piece of redwood is very fragile across the grain. All of the redwood I’ve handled seems likely to split along a grain line if you flex it perpendicular to the grain lines. I call that splitty. George Lowden uses soundhole reinforcements on most, if not all, of his marvelous guitars.
The trouble with this patch is, it needs to be a nice piece of wood. I don’t have any scraps that large, so it means cutting up a piece that might otherwise make a good guitar soundboard. Ugh. That’s a waste. I told my favorite engineer Karen about my problem and she suggested using one of the botched soundboards hanging on my wall. Eureka. A new trademark feature: the double rosette soundboard. Here’s how it all went:
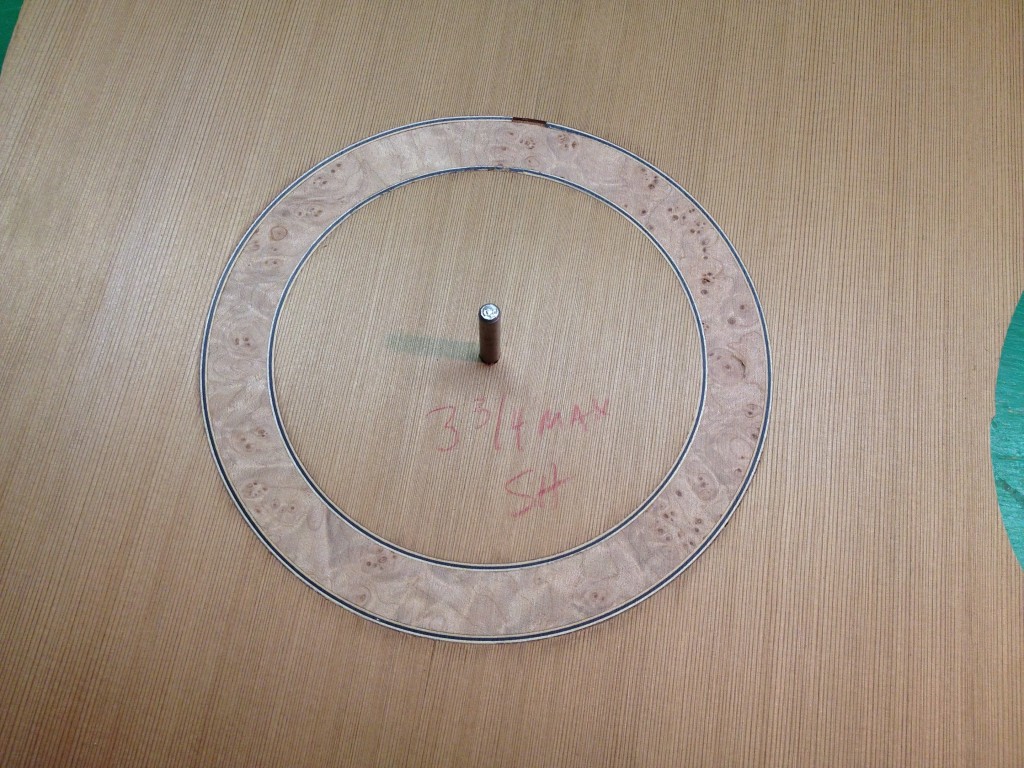
The donor soundboard. Some fine Western Red Cedar that was thinned a little too much. Beautiful maple burl rosette, same as on my daughter’s 0 style.
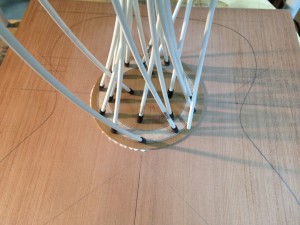
Using the circle-routing jig’s board and pin to align the two pieces. The white sticks, part of a go-bar deck, are the clamps,

Gratuitous photo of the pretty rosette, taken for posterity in case I botch the top when cutting out the soundhole.

Cutting out the soundhole. Set the depth for a very shallow cut and turn it slowly. Make a few routs and then turn the top over to go at it from the back side. The cuts meet in the middle.
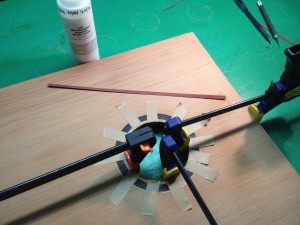
Gluing in the soundhole trim ring. This is a thin piece of bloodwood. The small piece there next the glue bottle is identical to the one being glued. It will be added to make the ring thicker when this glue-up is dry.
I like this new trademark style of yours. But question–once you run out of botched tops that you have saved, and once you stop botching tops, then how will you continue this AWESOME trademark idea?? You are getting better and better with your skill and making fewer and fewer mistakes, so I am just sayin’… Thanks for the engineering credit though!
Stop Botching Tops. Say that six times real fast. You assume some sort of progress, but I gotta say I haven’t let that worry me too much.
Now if I botch this board, can I cut out its double rosette to reinforce the next top and thus have a triple rosette top? Hmmm…